Lilemong tsa morao tjena, ka lebaka la tsoelo-pele e potlakileng ea indasteri e ncha ea matla, laser welding e kene ka potlako indastering eohle e ncha ea matla ka lebaka la melemo ea eona e potlakileng le e tsitsitseng. Har'a tsona, lisebelisoa tsa ho cheselletsa laser li ikarabella bakeng sa karolo e phahameng ka ho fetisisa ea ts'ebeliso indastering eohle e ncha ea matla.
Ho chesoa ka laserka potlako e fetohile khetho ea pele likarolong tsohle tsa bophelo ka lebaka la lebelo la eona le potlakileng, botebo bo boholo, le ho senyeha ho honyenyane. Ho tloha ho li-welld ho ea ho li-welds tsa butt, li-buildup le li-welds tsa seal,laser tjheseletsae fana ka nepo le taolo e ke keng ea lekanngoa. E bapala karolo ea bohlokoa tlhahisong ea indasteri le tlhahisong, ho kenyeletsoa indasteri ea sesole, tlhokomelo ea bongaka, sebaka sa sefofane, likarolo tsa koloi tsa 3C, tšepe ea mochini, matla a macha le liindasteri tse ling.
Ha ho bapisoa le mahlale a mang a tjheseletsa, laser welding e na le melemo le mathata a eona a ikhethang.
Molemo:
1. Lebelo le potlakileng, botebo bo boholo le deformation e nyane.
2. Welding e ka etsoa ka mocheso o tloaelehileng kapa tlas'a maemo a khethehileng, 'me thepa ea ho tjheseletsa e bonolo. Ka mohlala, lebone la laser ha le hoholehe sebakeng sa makenete ea motlakase. Li-Laser li ka tjheseletsa ka har'a vacuum, moea kapa tikolohong e itseng ea khase, 'me li ka cheseletsa lisebelisoa tse ka khalase kapa tse pepeneneng ho lebaleng la laser.
3. E khona ho cheselletsa lisebelisoa tsa refractory tse kang titanium le quartz, hape e ka cheselletsa lisebelisoa tse sa tšoaneng ka litholoana tse ntle.
4. Ka mor'a hore laser e tsepamise maikutlo, matla a matla a matla a phahame. Karo-karolelano e ka fihla ho 5: 1, 'me e ka fihla ho 10: 1 ha ho chesetsoa lisebelisoa tse matla a phahameng.
5. Micro welding e ka etsoa. Ka mor'a hore lebone la laser le tsepame, ho ka fumanoa sebaka se senyenyane 'me se ka behoa ka nepo. E ka sebelisoa ho kopanya le ho cheselletsa li-workpieces tse nyane le tse nyane ho fihlela tlhahiso ea boima bo ikemetseng.
6. E ka cheselletsa libaka tseo ho leng thata ho fihla ho tsona 'me ea etsa welding ea sebaka se selelele e sa amaneng le eona, ka bonolo bo boholo. Haholo-holo lilemong tsa morao tjena, theknoloji ea ts'ebetso ea laser ea YAG e amohetse theknoloji ea optical fiber transmission, e nolofalitseng theknoloji ea welding ea laser ho khothaletsoa le ho sebelisoa haholo.
7. Lebone la laser le bonolo ho arola ka nako le sebaka, 'me maballo a mangata a ka sebetsanoa libakeng tse ngata ka nako e le' ngoe, a fana ka maemo bakeng sa welding e nepahetseng haholoanyane.
Bothata:
1. Ho nepahala ha kopano ea workpiece ho hlokahala hore e be holimo, 'me boemo ba sefate holim'a workpiece bo ke ke ba kheloha haholo. Lebaka ke hobane boholo ba letheba la laser ka mor'a ho tsepamisa maikutlo bo nyane mme seam sa weld se moqotetsane, se etsa hore ho be thata ho eketsa lisebelisoa tsa tšepe tsa filler. Haeba ho nepahala ha kopano ea workpiece kapa boemo bo nepahetseng ba sefahla bo sa finyelle litlhoko, mefokolo ea welding e atisa ho etsahala.
2. Litsenyehelo tsa li-lasers le litsamaiso tse amanang le tsona li phahame, 'me letsete la nako e le' ngoe le leholo.
Litšitiso tse tloaelehileng tsa laser weldingka tlhahiso ea betri ea lithium
1. Welding porosity
Litšitiso tse tloaelehileng holaser tjheseletsake li-pores. Letamo la ho tjheseletsa le tjheseletsang le tebile ebile le patisane. Nakong ea ts'ebetso ea laser welding, naetrojene e hlasela letamo le qhibilihisitsoeng ka ntle. Nakong ea ho bata le ho tiisa ts'ebetso ea tšepe, ho qhibiliha ha naetrojene ho fokotseha ka ho fokotseha ha mocheso. Ha tšepe e qhibilihisitsoeng ea letamo e pholile ho qala ho crystallize, , solubility e tla theoha haholo le ka tšohanyetso. Ka nako ena, khase e ngata e tla potlaka ho etsa li-bubble. Haeba lebelo le phaphametseng la li-bubble le le tlase ho lebelo la crystallization ea tšepe, li-pores li tla hlahisoa.
Lits'ebetsong indastering ea betri ea lithium, hangata re fumana hore li-pores li ka etsahala haholo nakong ea ho chesoa ha eleketrode e ntle, empa hangata ha li etsahale nakong ea ho cheselletsa electrode e mpe. Sena ke hobane electrode e ntle e entsoe ka aluminium le electrode e mpe e entsoe ka koporo. Nakong ea ho cheselletsa, aluminium ea metsi e holim'a metsi e fokotsehile pele khase e ka hare e phalla ka ho feletseng, e thibela khase hore e se ke ea phalla le ho etsa masoba a maholo le a manyenyane. Stomata e nyane.
Ho phaella ho lisosa tsa li-pores tse boletsoeng ka holimo, li-pores li boetse li kenyelletsa moea o ka ntle, mongobo, oli ea holim'a metsi, joalo-joalo Ho phaella moo, tataiso le angle ea ho fofa ha naetrojene e tla boela e ama ho thehoa ha li-pores.
Mabapi le mokhoa oa ho fokotsa ho hlaha ha li-pores tsa welding?
Pele, peletjheseletsa, matheba a oli le litšila holim'a lisebelisoa tse kenang li hloka ho hloekisoa ka nako; tlhahiso ea libeteri tsa lithium, tlhahlobo ea thepa e kenang ke ts'ebetso ea bohlokoa.
Ea bobeli, phallo ea khase e sireletsang e lokela ho fetoloa ho latela lintlha tse kang lebelo la welding, matla, boemo, joalo-joalo, 'me ha ea lokela ho ba kholo haholo kapa e nyane haholo. Khatello ea seaparo se sireletsang e lokela ho fetoloa ho latela lintlha tse kang matla a laser le boemo ba ho tsepamisa maikutlo, 'me ha ea lokela ho ba holimo haholo kapa tlaase haholo. Sebopeho sa nozzle ea seaparo se sireletsang se lokela ho fetoloa ho ea ka sebopeho, tataiso le lintlha tse ling tsa weld e le hore seaparo se sireletsang se ka koahela sebaka sa welding ka tsela e tšoanang.
Ea boraro, laola mocheso, mongobo le lerōle moeeng ka har'a workshop. Thempereichara ea tikoloho le mongobo li tla ama boemo ba mongobo holim'a substrate le khase e sireletsang, e leng eona e tla ama ho hlahisa le ho phonyoha ha mouoane oa metsi ka letamong le qhibilihileng. Haeba mocheso oa mocheso le mongobo o phahame haholo, ho tla ba le mongobo o mongata holim'a substrate le khase e sireletsang, e hlahisang mouoane o mongata oa metsi, o hlahisang li-pores. Haeba mocheso le mongobo o teng o le tlase haholo, ho tla ba le mongobo o fokolang haholo holim'a substrate le khase e sireletsang, ho fokotsa ho hlahisa mouoane oa metsi, kahoo ho fokotsa li-pores; tlohella basebetsi ba boleng hore ba lemohe boleng ba sepheo sa mocheso, mongobo le lerōle seteisheneng sa welding.
Ntlha ea bone, mokhoa oa ho phunya o sebelisoa ho fokotsa kapa ho felisa li-pores ka laser deep penetration welding. Ka lebaka la ho eketsoa ha seketsoana nakong ea ho tjheseletsa, ho fetoha ha sefate ho ea ho seam ho etsa hore ho be le ho tsosolosoa khafetsa ha karolo ea seam ea weld, e leng ho lelefatsang nako ea ho lula ha tšepe ea metsi ka letamo la welding. Ka nako e ts'oanang, ho kheloha ha sefate ho boetse ho eketsa mocheso oa mocheso sebakeng sa lihlopha. Karolelano ea botebo-ho-bophara ba weld e fokotsehile, e leng se loketseng ho hlaha ha li-bubble, ka hona ho felisa li-pores. Ka lehlakoreng le leng, ho sisinyeha ha sekoti ho etsa hore lesoba le lenyenyane le tsubelle ka tsela e nepahetseng, e leng se ka fanang ka matla a susumetsang bakeng sa letamo la ho cheselletsa, ho eketsa convection le ho sisinyeha ha letamo la ho cheselletsa, 'me ho na le phello e molemo ho felisa li-pores.
Ea bohlano, maqhubu a pulse, frequency ea pulse e bua ka palo ea likhahla tse hlahisoang ke beam ea laser ka nako ea yuniti, e tla ama tlhahiso ea mocheso le ho bokellana ha mocheso ka letamong le entsoeng ka ho qhibilihisoa, ebe e ama tšimo ea mocheso le tšimo ea phallo e qhibilihisitsoeng. letamo. Haeba maqhubu a pulse a phahame haholo, a tla lebisa ho kenngoa ha mocheso o feteletseng ka letamong le qhibilihisitsoeng, ho etsa hore mocheso oa letamo le qhibilihisitsoeng o be o phahameng haholo, o hlahisang mouoane oa tšepe kapa likarolo tse ling tse sa tsitsang ka mocheso o phahameng, o bakang li-pores. Haeba maqhubu a pulse a le tlase haholo, a tla lebisa ho bokelleng ha mocheso o sa lekaneng ka letamong le qhibilihisitsoeng, ho etsa hore mocheso oa letamo le qhibilihisitsoeng o be tlase haholo, ho fokotsa ho qhibiliha le ho phonyoha ha khase, ho fella ka pores. Ka kakaretso, maqhubu a pulse a lokela ho khethoa ka har'a sebaka se lekaneng se ipapisitseng le botenya ba substrate le matla a laser, 'me u qobe ho ba holimo haholo kapa tlase haholo.
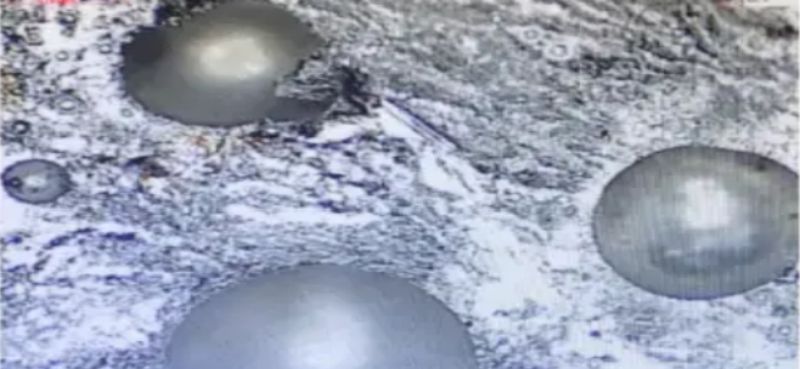
Likoti tsa ho tjheseletsa (ho tjheseletsa ka laser)
2. Weld spatter
Spatter e hlahisoang nakong ea ts'ebetso ea welding, welding laser e tla ama boleng ba bokaholimo ba weld, 'me e tla silafatsa le ho senya lense. Ts'ebetso e akaretsang ke e latelang: ka mor'a hore welding ea laser e phethoe, likaroloana tse ngata tsa tšepe li hlaha holim'a thepa kapa mosebetsi oa matsoho 'me li khomarele holim'a thepa kapa mosebetsi. Ts'ebetso e hlakileng ka ho fetesisa ke hore ha ho cheselletsa ka mokhoa oa galvanometer, kamora nako ea ts'ebeliso ea lense e sirelletsang ea galvanometer, ho tla ba le likoti tse teteaneng holim'a metsi, 'me likoting tsena li bakoa ke ho cheselletsa spatter. Ka mor'a nako e telele, ho bonolo ho thibela leseli, 'me ho tla ba le mathata ka leseli la welding, e leng se tla fella ka letoto la mathata a kang ho robeha ho tjheseletsa le ho tjheseletsa ka sebele.
Lisosa tsa ho fafatsa ke life?
Ntlha ea pele, matla a matla, matla a maholo a matla, ho bonolo ho hlahisa spatter, 'me spatter e amana ka ho toba le matla a matla. Bona ke bothata ba lilemo tse lekholo. Bonyane ho fihlela joale, indasteri ha e khone ho rarolla bothata ba ho phatloha, 'me e ka bolela feela hore e fokotsehile hanyenyane. Indastering ea betri ea lithium, ho phatloha ke sesosa se seholo sa potoloho e khuts'oane ea betri, empa ha e so khone ho rarolla sesosa. Tšusumetso ea spatter ho betri e ka fokotsoa feela ho tloha ntlheng ea ts'ireletso. Mohlala, selikalikoe sa likou tsa ho tlosa lerōle le likoahelo tse sireletsang li eketsoa ho potoloha karolo ea welding, 'me mela ea lithipa tsa moea e eketsoa ka selikalikoe ho thibela tšusumetso ea spatter kapa esita le tšenyo ea betri. Ho senya tikoloho, lihlahisoa le likarolo tse pota-potileng seteishene sa ho tjheseletsa ho ka boleloa hore ho felisitse mekhoa.
Ha e le ho rarolla bothata ba spatter, ho ka boleloa feela hore ho fokotsa matla a ho chesa ho thusa ho fokotsa spatter. Ho fokotsa lebelo la welding ho ka boela ha thusa haeba ho kenella ho sa lekana. Empa litlhoko tse ling tse khethehileng tsa ts'ebetso, ha e na phello e fokolang. Ke ts'ebetso e ts'oanang, mechini e fapaneng le lihlopha tse fapaneng tsa lisebelisoa li na le litlamorao tse fapaneng tsa welding. Ka hona, ho na le molao o sa ngoloang indastering e ncha ea matla, sete e le 'ngoe ea litekanyetso tsa welding bakeng sa sesebelisoa se le seng.
Ntlha ea bobeli, haeba bokaholimo ba thepa e entsoeng kapa mosebetsi o sa hloekisoe, litšila tsa oli kapa litšila le tsona li tla baka ho phatloha ho hoholo. Nakong ena, ntho e bonolo ka ho fetisisa ke ho hloekisa bokaholimo ba thepa e entsoeng.
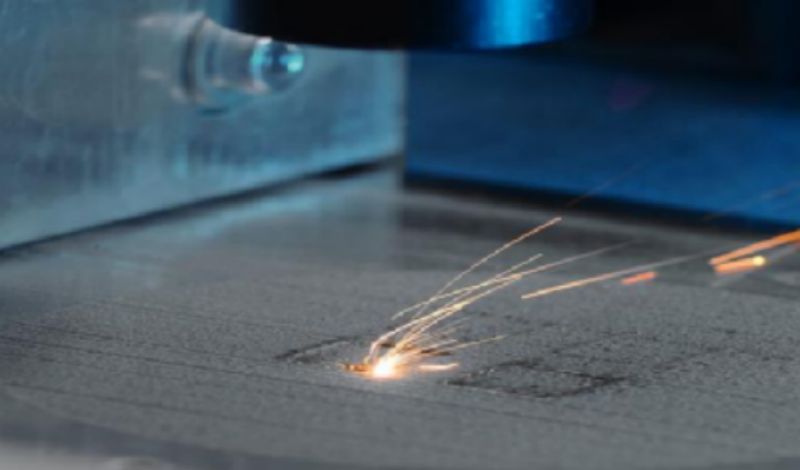
3. High reflectivity ea laser tjheseletsa
Ka kakaretso, ponahatso e phahameng e bua ka taba ea hore thepa ea ho sebetsa e na le mohanyetsi o monyane, sebaka se batlang se boreleli, le sekhahla se tlase sa ho monya bakeng sa li-laser tse haufi tsa infrared, tse lebisang ho tlhahiso e ngata ea laser, le hobane ho sebelisoa li-lasers tse ngata. e otlolohileng Ka lebaka la lintho tse bonahalang kapa tšekamelo e nyenyane, lebone la laser le khutlang le kena hape hloohong ea tlhahiso, esita le karolo ea leseli le khutlang e kopanngoa le fiber e fetisang matla, 'me e fetisetsoa morao hammoho le fiber ho ea ka hare. ea laser, ho etsa hore likarolo tsa mantlha ka har'a laser li tsoele pele ho ba mocheso o phahameng.
Ha reflectivity e phahame haholo nakong ea welding ea laser, ho ka nkoa litharollo tse latelang:
3.1 Sebelisa anti-reflection coat kapa tšoara holim'a thepa: ho roala holim'a thepa ea ho tjheseletsa ka lesela le khahlanong le ho bonahatsa ho ka fokotsa ka katleho ho bonahatsa laser. Ho roala hona hangata ke thepa e khethehileng ea optical e nang le reflectivity e tlaase e monyang matla a laser ho e-na le ho e khutlisetsa morao. Lits'ebetsong tse ling, joalo ka welding ea hona joale ea mokelli, khokahano e bonolo, joalo-joalo, bokaholimo le bona bo ka beoa.
3.2 Fetola angle ea ho tjheseletsa: Ka ho lokisa sekhutlo sa welding, lebone la laser le ka ba ketsahalong ea lisebelisoa tsa welding ka lehlakoreng le nepahetseng le ho fokotsa ketsahalo ea ho bonahatsa. Ka tloaelo, ho ba le ketsahalo ea beam laser perpendicularly ho ea holim'a thepa e lokelang ho chesetsoa ke mokhoa o motle oa ho fokotsa ho bonahatsa.
3.3 Ho eketsa mokelikeli o thusang: Nakong ea ts'ebetso ea welding, palo e itseng ea motsoako o thusang, o kang phofo kapa metsi, o kenngoa ho weld. Li-absorber tsena li monya matla a laser le ho fokotsa ho bonahatsa. Motsoako o loketseng o hloka ho khethoa ho latela lisebelisoa tse khethehileng tsa welding le maemo a kopo. Ka indasteri ea betri ea lithium, sena ha se khonehe.
3.4 Sebelisa fiber ea optical ho fetisetsa laser: Haeba ho khoneha, fiber ea optical e ka sebelisoa ho fetisetsa laser sebakeng sa welding ho fokotsa ho bonahatsa. Li-fiber tsa optical li ka tataisa beam ea laser sebakeng sa welding ho qoba ho pepeseha ka kotloloho holim'a lisebelisoa tsa welding le ho fokotsa ho hlaha ha likhakanyo.
3.5 Ho fetola li-parameter tsa laser: Ka ho lokisa li-parameter tse kang matla a laser, bolelele ba tsepamiso, le bophara bo tsepamisitsoeng, kabo ea matla a laser e ka laoloa 'me lipontšo li ka fokotsoa. Bakeng sa lisebelisoa tse ling tse bonahatsang, ho fokotsa matla a laser e ka ba mokhoa o sebetsang oa ho fokotsa likhakanyo.
3.6 Sebelisa sekhechana sa boriti: Sekhahla sa beam se ka tataisa karolo ea matla a laser ho sesebelisoa sa ho monya, ka hona se fokotsa ho hlaha ha lipontšo. Lisebelisoa tsa ho arola li-beam hangata li na le likarolo tsa optical le li-absorber, 'me ka ho khetha likarolo tse loketseng le ho lokisa sebopeho sa sesebelisoa, ho ka finyelloa ho fokotseha ho tlaase.
4. Welding undercut
Ts'ebetsong ea tlhahiso ea betri ea lithium, ke lits'ebetso life tse ka 'nang tsa baka ho fokotseha? Hobaneng ha undercutting e etsahala? A re e hlahlobeng.
Undercut, ka kakaretso lisebelisoa tse tala ha li kopane hantle, lekhalo le leholo haholo kapa groove e hlaha, botebo le bophara bo boholo ho feta 0.5mm, bolelele bohle bo feta 10% ea bolelele ba weld, kapa e kholo ho feta tekanyetso ea ts'ebetso ea sehlahisoa bolelele bo kopiloeng.
Ts'ebetsong eohle ea tlhahiso ea betri ea lithium, ho ka etsahala hore ho fokotsehe ho ka etsahala, 'me ka kakaretso ho ajoa ka ho tiisa pele ho tjheseletsa le ho tjheseletsa ha poleiti ea sekoahelo sa cylindrical le ho tiisa pele ho tjheseletsa le ho tjheseletsa ha poleiti ea sekoahelo sa aluminium sekoahelo. Lebaka le ka sehloohong ke hore sekoaelo sa sekoaelo se hloka ho sebelisana 'moho le khetla ho Welding, ts'ebetso e ts'oanang lipakeng tsa sekoaelo sa sekoaelo le khetla e na le likheo tse feteletseng tsa weld, li-grooves, ho putlama, joalo-joalo, ka hona e na le menyetla e mengata haholo. .
Joale ke eng e bakang undercutting?
Haeba lebelo la tjheseletsa le potlakile haholo, tšepe ea mokelikeli ka mor'a lesoba le lenyenyane le supang bohareng ba tjheseletsa e ke ke ea ba le nako ea ho arola bocha, e leng se etsang hore ho be le solidification le undercutting mahlakoreng ka bobeli a weld. Ka lebaka la boemo bo ka holimo, re hloka ho ntlafatsa li-parameter tsa welding. Ka mantsoe a bonolo, ho etsoa liteko tse pheta-phetoang ho netefatsa liparamente tse fapaneng, 'me u tsoele pele ho etsa DOE ho fihlela li-parameter tse nepahetseng li fumanoa.
2. Likheo tse feteletseng tsa weld, li-grooves, collapses, joalo-joalo tsa lisebelisoa tsa ho tjheseletsa li tla fokotsa palo ea tšepe e qhibilihisitsoeng e tlatsang likheo, ho etsa hore li-undercuts li ka etsahala. Ena ke potso ea lisebelisoa le lisebelisoa tse tala. Ho sa tsotellehe hore na lisebelisoa tse tala tsa welding li finyella litlhoko tse kenang tsa lisebelisoa tsa ts'ebetso ea rona, hore na ho nepahala ha thepa ho finyella litlhoko, joalo-joalo Tloaelo e tloaelehileng ke ho hlokofatsa kamehla le ho otla bafani ba thepa le batho ba laolang thepa.
3. Haeba matla a theoha ka potlako qetellong ea laser welding, lesoba le lenyenyane le ka 'na la putlama, e leng se etsang hore ho be le undercutting ea sebaka seo. Ho lumellana ho nepahetseng ha matla le lebelo ho ka thibela ka katleho ho thehoa ha li-undercuts. Joalo ka ha polelo ea khale e tsoela pele, pheta liteko, netefatsa liparamente tse fapaneng, 'me u tsoele pele DOE ho fihlela u fumana liparamente tse nepahetseng.
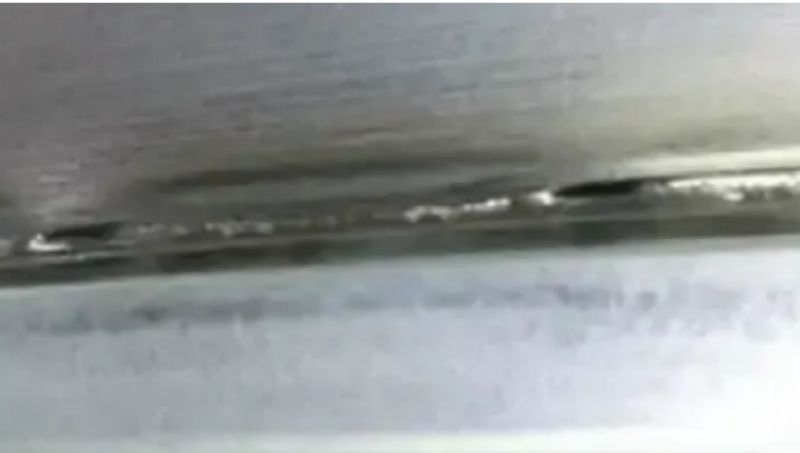
5. Weld center e putlama
Haeba lebelo la tjheseletsa le lieha, letamo le qhibilihisitsoeng le tla ba le leholo le le leholo, le eketsa palo ea tšepe e qhibilihisitsoeng. Sena se ka etsa hore ho be thata ho boloka tsitsipano holimo. Ha tšepe e qhibilihisitsoeng e e-ba boima haholo, karolo e bohareng ea cheseletso e ka ’na ea teba ’me ea etsa li-dips le mekoti. Tabeng ena, matla a motlakase a lokela ho fokotsoa ka nepo ho thibela ho putlama ha metsi.
Boemong bo bong, lekhalo la tjheseletsa le etsa ho putlama ntle le ho baka ho phatloha. Ha ho pelaelo hore sena ke bothata ba lisebelisoa tsa mochine oa khatiso.
Kutloisiso e nepahetseng ea mefokolo e ka bang teng nakong ea welding ea laser le lisosa tsa likoli tse fapaneng li lumella mokhoa o lebisitsoeng ho feta oa ho rarolla mathata leha e le afe a sa tloaelehang a tjheseletsa.
6. Mapetsong a cheseletso
Mapetso a hlahang nakong ea ho cheseletsa ka laser e tsoelang pele haholo-holo ke mapetsong a mocheso, a kang mapetsong a kristale le mapetsong a liquefaction. Lebaka le ka sehloohong la mapetsong ana ke matla a maholo a ho fokotseha a hlahisoang ke weld pele e tiisa ka ho feletseng.
Hape ho na le mabaka a latelang a ho phatloha ha laser welding:
1. Moralo o sa utloahaleng oa weld: Moralo o sa nepahalang oa geometry le boholo ba weld o ka baka khatello ea khatello ea maikutlo, ka hona e baka mapetsong. Tharollo ke ho ntlafatsa moralo oa weld ho qoba khatello ea maikutlo ea welding. U ka sebelisa li-welds tse nepahetseng tsa offset, fetola sebopeho sa weld, joalo-joalo.
2. Ho se lumellane ha li-parameter tsa welding: Khetho e sa nepahalang ea li-welding parameters, tse kang lebelo la ho tjheseletsa ka potlako, matla a phahameng haholo, joalo-joalo, li ka lebisa ho fetoha ha mocheso o sa lekaneng sebakeng sa ho tjheseletsa, ho baka khatello e kholo ea ho tjheseletsa le mapetsong. Tharollo ke ho lokisa liparamente tsa welding hore li tsamaellane le thepa e itseng le maemo a welding.
3. Tlhophiso e mpe ea sebaka sa welding: Ho hloleha ho hloekisa hantle le pele ho ts'oaroa sebaka sa welding pele ho tjheseletsa, joalo ka ho tlosa li-oxides, grease, joalo-joalo, ho tla ama boleng le matla a weld le ho lebisa mapetsong habonolo. Tharollo ke ho hloekisa ka ho lekaneng le pele ho tšoara sebaka sa welding ho etsa bonnete ba hore litšila le litšila sebakeng sa welding li tšoaroa ka katleho.
4. Taolo e sa nepahalang ea ho kenya mocheso oa welding: Taolo e fosahetseng ea ho kenya mocheso nakong ea welding, joalo ka mocheso o feteletseng nakong ea welding, tekanyo e sa lokelang ea ho pholisa ea lera la welding, joalo-joalo, e tla lebisa liphetohong tsa sebopeho sa sebaka sa welding, se hlahisang mapetsong. . Tharollo ke ho laola mocheso le sekhahla sa ho pholisa nakong ea ho cheselletsa ho qoba mocheso o feteletseng le ho bata ka potlako.
5. Phokotso e sa lekaneng ea khatello ea maikutlo: Phekolo e sa lekaneng ea ho imolla khatello ea maikutlo ka mor'a ho tjheseletsa ho tla fella ka ho se lekane ha khatello ea kelello sebakeng se cheselitsoeng, se tla lebisa habonolo mapetsong. Tharollo ke ho etsa phekolo e nepahetseng ea ho imolla khatello ea kelello ka mor'a ho cheselletsa, joalo ka phekolo ea mocheso kapa phekolo ea vibrate (lebaka le ka sehloohong).
Ha e le ts'ebetso ea tlhahiso ea libeteri tsa lithium, ke mekhoa efe e ka 'nang ea baka mapetsong?
Ka kakaretso, mapetsong a atisa ho etsahala nakong ea ho tiisa tjheseletsa, joalo ka ho tiisa tjheseletsa ea likhetla tsa tšepe tsa cylindrical kapa likhetla tsa aluminium, ho tiisa tjheseletsa ea likhetla tsa aluminium lisekoere, joalo-joalo Ho phaella moo, nakong ea ts'ebetso ea ho kenya mochine, ho tjheseletsa ha mokelli oa hona joale ho boetse ho tloaelehile. ho mapetsong.
Ehlile, re ka sebelisa terata ea ho tlatsa, preheating kapa mekhoa e meng ho fokotsa kapa ho felisa mapetsong ana.
Nako ea poso: Sep-01-2023